Table of contents
In the ever-evolving world of manufacturing, optimizing productivity remains at the forefront of competitive strategy. Rebuilt CNC lathes and milling machines offer a cost-effective and reliable pathway towards achieving higher efficiency and output. Explore how integrating rebuilt equipment can transform operations and unlock new levels of performance in your facility, revealing techniques and insights that can reshape your productivity landscape.
Unlocking Hidden Potential
Rebuilt CNC machines present a viable path to unlocking untapped capacity within existing manufacturing processes. Through machine tool refurbishment—an advanced approach involving CNC retrofitting and strategic upgrades—older CNC lathes and milling machines can be transformed to deliver enhanced performance that rivals new equipment. This process not only extends the operational lifespan of valuable assets but also results in cost-effective machining, significantly reducing the financial burden compared to purchasing new machinery. Facilities can leverage these improvements to boost manufacturing productivity, achieve tighter tolerances, and integrate updated controls or automation features. The lead manufacturing engineer at the facility is encouraged to elaborate on their experience, providing deeper insight into how machine tool refurbishment elevates both efficiency and output quality without the need for large-scale capital investment.
Advanced Automation Integration
Rebuilt CNC lathes and milling machines offer significant advantages by enabling the smooth incorporation of modern CNC automation solutions. Through a process known as automation retrofit, these machines can be equipped with advanced controls, sensors, and interfaces that support the integration of robotics in machining and other state-of-the-art industrial automation technologies. Rebuilt machine integration allows existing equipment to communicate efficiently with robotic arms, automated material handling systems, and intelligent monitoring platforms, all of which help modern machining environments achieve faster cycle times, higher accuracy, and improved consistency. The adaptability of rebuilt CNC equipment also supports seamless upgrades, ensuring compatibility with evolving production requirements and facilitating the transition to smart manufacturing systems. Collaborating with automation specialists during the automation retrofit process ensures that each machine is tailored to the specific needs of the operation, unlocking new levels of productivity and allowing manufacturers to stay competitive in a rapidly changing technological landscape.
Extending Machine Lifespan
Extending the operational life of CNC lathes and milling machines through professional rebuilding begins with a comprehensive assessment of each machine’s mechanical and electronic components. By refurbishing worn parts, replacing outdated controls, and realigning structural elements, the machine rebuild process restores and often enhances the performance of legacy equipment. Predictive maintenance, implemented as part of this strategy, enables the detection of potential failures before they result in unscheduled downtime. The shop’s maintenance manager highlights how this proactive approach not only ensures extended equipment lifespan but also supports consistent CNC machine longevity. Integrating predictive and preventive maintenance routines reduces downtime by streamlining troubleshooting and ensuring that issues are resolved before they escalate. As a result, rebuilt CNC machinery operates with increased reliability, maximizing productivity while optimizing the return on capital investment. This systematic focus on longevity and performance makes professional rebuilding a strategic solution for manufacturers aiming to maintain competitive efficiency with legacy equipment.
Boosting Precision And Quality
Upgrading CNC lathes and milling machines through advanced subsystems and precise alignments directly amplifies machining precision, ensuring every component produced meets elevated standards of accuracy. Rebuilt CNC accuracy stems from meticulous geometric calibration, which corrects axis deviations and spindle runout, thus minimizing dimensional errors and maximizing repeatability. This rigorous attention to alignment not only improves surface finish but also significantly reduces post-processing requirements, leading to a noticeable quality improvement in finished parts. As a result, customer satisfaction increases, driven by consistent part uniformity and high-performance applications. Quality control supervisors are encouraged to verify geometric calibration protocols and monitor surface finish metrics closely, as these measures underpin product excellence. Many companies turn to experienced providers like SAMO for specialized rebuilding services, benefiting from their expertise in enhancing both CNC calibration and overall productivity.
Maximizing Return On Investment
Selecting rebuilt CNC lathes and milling machines delivers compelling economic benefits for manufacturers seeking to optimize their CNC investment. One immediate advantage lies in cost savings, as rebuilt equipment demands a significantly lower upfront capital outlay compared to new machinery. This reduction enables financial controllers to improve capital expenditure optimization by allocating funds more strategically within the manufacturing budget. Shorter payback periods become achievable due to the minimized initial investment and the rapid deployment of high-performance rebuilt machines. Enhanced asset utilization follows, since existing infrastructure and operator expertise can often be leveraged with rebuilt CNC systems, minimizing downtime and transition costs. Ultimately, a well-executed rebuild ROI strategy enables manufacturers to maximize returns while maintaining operational efficiency, making rebuilt CNC solutions a prudent path for enterprises focused on sustainable, cost-effective production outcomes.
Similar articles
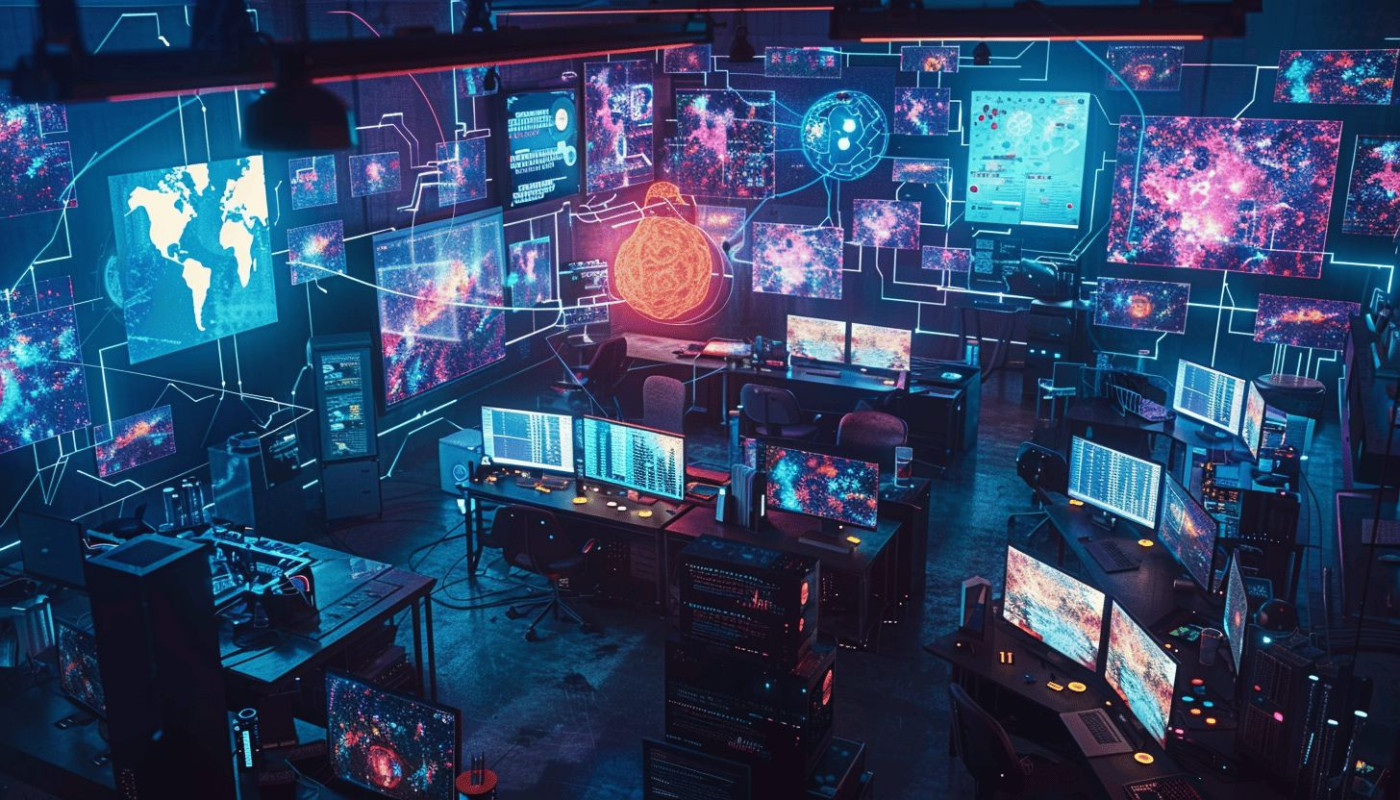
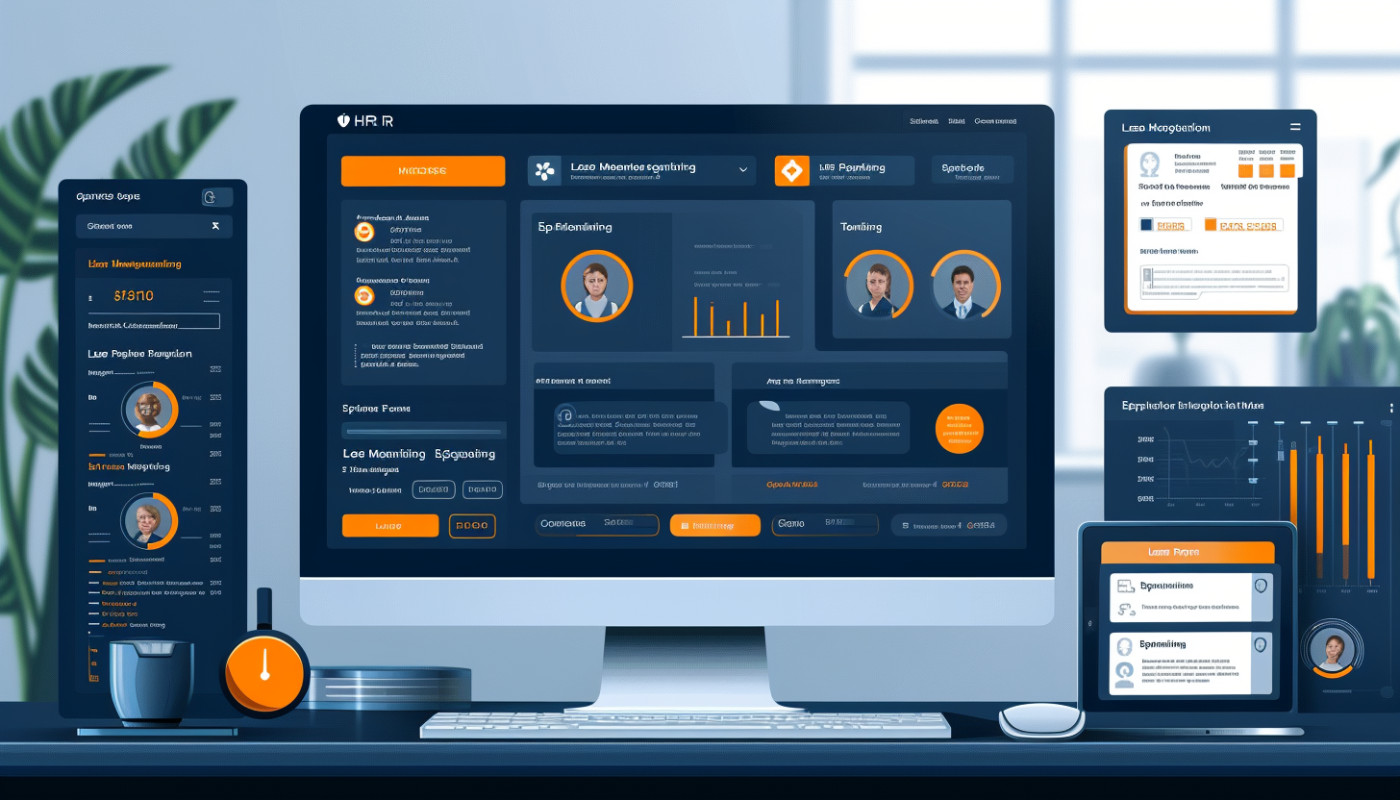
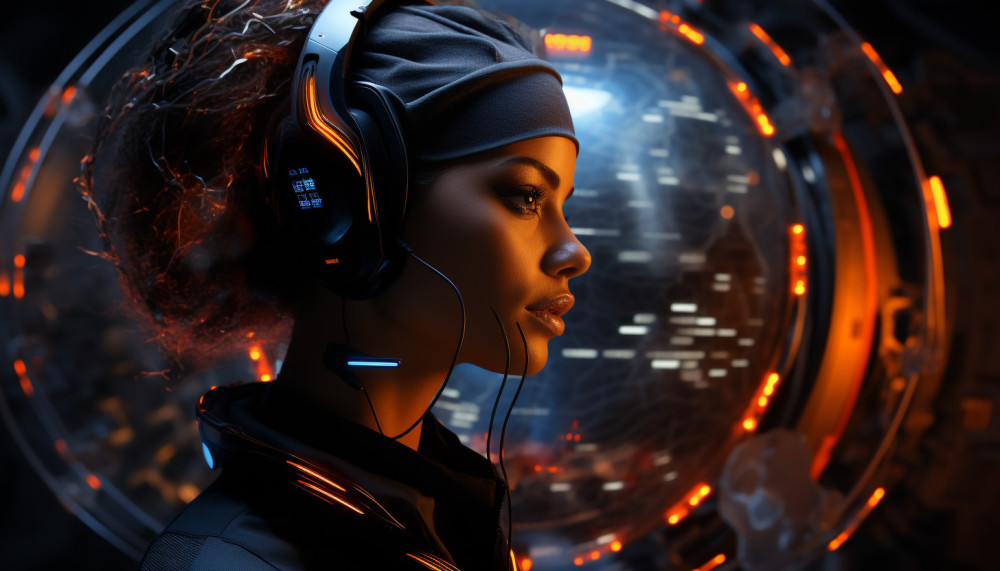